Custom plastic extrusion tailored to your industry needs
Custom plastic extrusion tailored to your industry needs
Blog Article
A Comprehensive Guide to the Process and Advantages of Plastic Extrusion
In the substantial realm of manufacturing, plastic extrusion emerges as a necessary and highly efficient process. Altering raw plastic into constant profiles, it caters to a variety of industries with its amazing versatility.
Recognizing the Essentials of Plastic Extrusion
While it might show up facility at first look, the process of plastic extrusion is essentially straightforward. The process starts with the feeding of plastic product, in the type of granules, powders, or pellets, right into a warmed barrel. The designed plastic is after that cooled, solidified, and reduced into preferred lengths, completing the procedure.
The Technical Process of Plastic Extrusion Explained

Sorts Of Plastic Suitable for Extrusion
The selection of the best kind of plastic is an essential element of the extrusion process. Different plastics use one-of-a-kind residential or commercial properties, making them much more matched to certain applications. Polyethylene, for instance, is typically used due to its low cost and easy formability. It supplies outstanding resistance to chemicals and dampness, making it optimal for items like tubes and containers. Polypropylene is an additional preferred selection due to its high melting point and resistance to exhaustion. For more robust applications, polystyrene and PVC (polyvinyl chloride) are usually selected for their strength and durability. These are typical alternatives, the option ultimately depends on the particular needs of the item being generated. So, understanding these plastic types can considerably improve the extrusion process.
Contrasting Plastic Extrusion to Various Other Plastic Forming Methods
Recognizing the kinds of plastic suitable for extrusion paves the means for a wider conversation on exactly how plastic extrusion compares to various other plastic developing approaches. These consist of shot molding, impact molding, and thermoforming. Each technique has its distinct uses and advantages. Shot molding, as an example, is exceptional for producing intricate parts, while strike molding is perfect for hollow objects like bottles. Thermoforming excels at forming huge or shallow parts. Nevertheless, plastic extrusion is unmatched when it comes to producing constant accounts, such as pipelines, gaskets, and seals. It likewise enables a regular cross-section along the length of the item. Therefore, the choice of Check This Out approach largely relies on the end-product requirements and specs.
Secret Advantages of Plastic Extrusion in Production
In the world of manufacturing, plastic extrusion provides lots of considerable advantages. One remarkable advantage is the cost-effectiveness of the process, that makes it an economically enticing production approach. Furthermore, this method supplies exceptional item flexibility and enhanced manufacturing rate, therefore boosting overall manufacturing effectiveness.
Economical Production Technique
Plastic extrusion jumps to the forefront as a cost-efficient production technique in production. This procedure stands out for its capacity to create high volumes of material promptly and efficiently, providing manufacturers with substantial savings. The key expense benefit is the ability to make use of less costly resources. Extrusion utilizes polycarbonate materials, which are less pricey contrasted to steels or ceramics. Additionally, the extrusion process itself is fairly easy, decreasing labor expenses. Additionally, plastic extrusion calls for less energy than conventional production techniques, contributing to lower operational costs. The procedure likewise decreases find more information waste, as any kind of faulty or excess products can be reused and recycled, supplying another layer of cost-effectiveness. Overall, the economic benefits make plastic extrusion a highly attractive choice in the production sector.
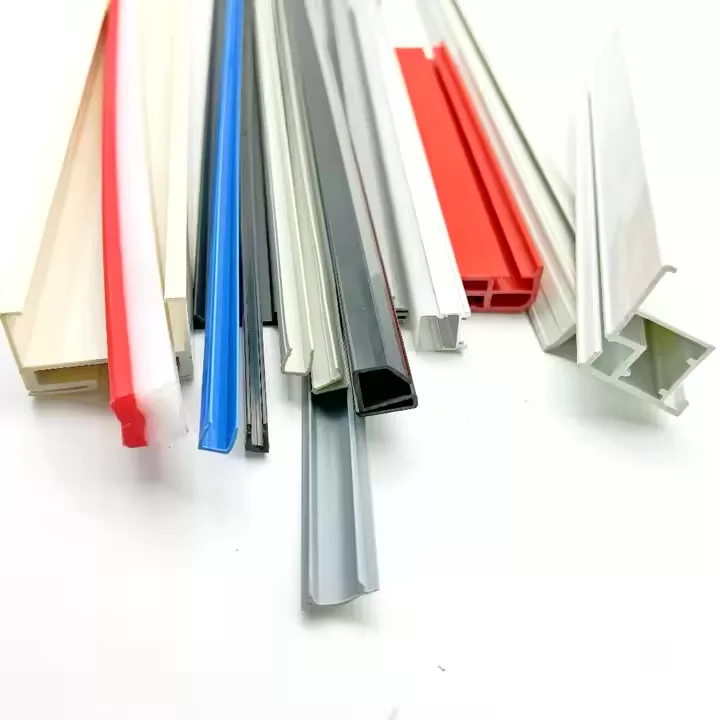
Superior Item Versatility
Beyond the cost-effectiveness of plastic extrusion, an additional significant benefit in manufacturing hinge on its remarkable product flexibility. This procedure permits for the production of a vast variety of products with varying dimensions, shapes, and layouts, from straightforward plastic sheets to complex accounts. The flexibility is credited to the extrusion die, which can be customized to yield the wanted product style. This makes plastic extrusion a perfect service for markets that require personalized plastic elements, such as automobile, building and construction, and packaging. The ability to create varied products is not only useful in conference particular market demands but additionally in enabling makers to check out new item lines with marginal capital expense. Fundamentally, plastic extrusion's item adaptability promotes innovation while improving operational performance.
Enhanced Manufacturing Speed
A substantial advantage of plastic extrusion lies in its improved production speed. Couple of various other manufacturing processes can match the rate of plastic extrusion. Furthermore, the ability to keep consistent high-speed manufacturing without sacrificing item high quality sets plastic extrusion apart from other methods.
Real-world Applications and Influences of Plastic Extrusion
In the realm of manufacturing, the method of plastic extrusion holds extensive relevance. The financial benefit of plastic extrusion, primarily its high-volume and economical result, has transformed manufacturing. The More about the author market is constantly aiming for technologies in naturally degradable and recyclable materials, indicating a future where the benefits of plastic extrusion can be preserved without compromising ecological sustainability.
Conclusion
In conclusion, plastic extrusion is a highly efficient and efficient approach of changing basic materials into diverse items. It offers many benefits over various other plastic creating approaches, consisting of cost-effectiveness, high output, very little waste, and layout versatility. Its influence is greatly felt in numerous industries such as building and construction, automobile, and consumer goods, making it a pivotal process in today's manufacturing landscape.
Diving much deeper right into the technical process of plastic extrusion, it begins with the choice of the appropriate plastic product. When cooled, the plastic is cut into the needed sizes or wound onto reels if the item is a plastic movie or sheet - plastic extrusion. Contrasting Plastic Extrusion to Various Other Plastic Forming Approaches
Comprehending the kinds of plastic suitable for extrusion leads the method for a more comprehensive conversation on just how plastic extrusion piles up against various other plastic forming approaches. Few various other production processes can match the rate of plastic extrusion.
Report this page